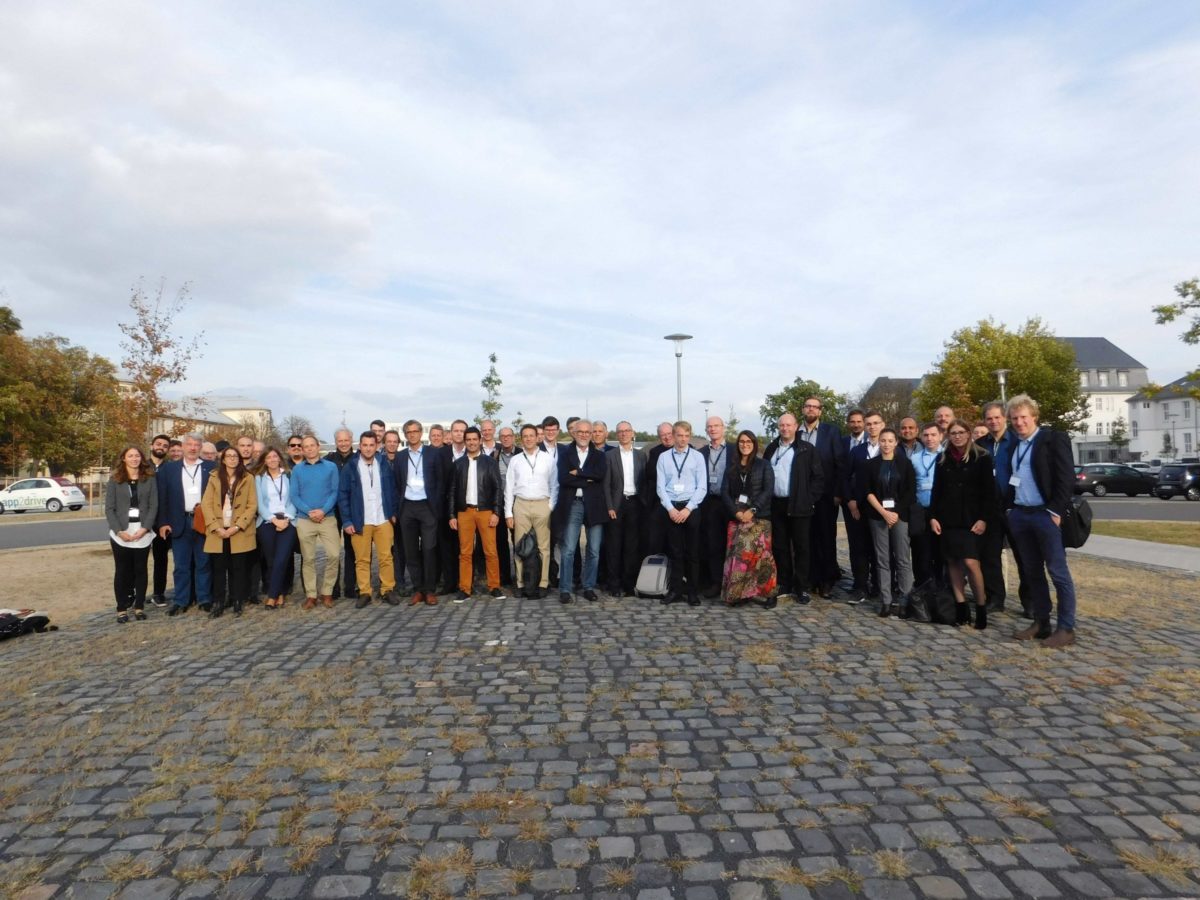
Simulation – Connecting the big picture with the details
Digital twins and simulation play an important role in Productive4.0. They allow for different scenarios in order to optimise the production or test completely new ways and processes without risking disruptions. In real life, unforeseen mistakes, asymmetric information and occurring problems may easily jeopardise the intended effect with constant adjustments eating time and burning money.
Even though simulation models in general are not new, they are still insufficient when it comes to map all potential processes and details that have to be taken into account when covering the process chain from back end to front end as well as the complete supply chain. This is why German chip producer Bosch, simulation software specialist Simplan and other project partners are working on a solution that allows combining the micro level with the macro level.
As a co leader, SimPlan is active in work package 4, developing tools that are needed in work package 5 where Bosch is the industrial leader and where SimPlan provides models as test bed. Simply put, SimPlan is designing simulation models for digital twins, and the application of the virtual production will then be tested and demonstrated in the Bosch semiconductor supply chain use case in work package 9.
New approach
In the following interview, SimPlan CEO Sven Spieckermann talks about the specific challenges and the new approach.
Mr. Spieckermann, how do you see your role in Productive4.0?
We intend to leverage the potentials of digitalisation and make simulations more straightforward with simulations, mainly addressing the digital production and supply chain network. The product life cycle management is less in the focus.
How come?
In a way, it has to do with the fact that it is challenging enough to model supply chains and process chains, from the global scale all the way down to single fabrication tools. So we are talking about macro models simulating all production plants in a supply chain including delivery conditions, periods and stocks on the one hand. On the other hand we have micro models which cover individual parts of the production like machines processing wafers, and which simulate conditions like utilisation rates, backlogs or bottlenecks.
Couldn’t you just enhance these models?
As a matter of fact, it is still not possible to put everything into one global simulation model without a loss of quality on one or the other side…which happens to be the main drawback of state-of-the-art models. Now the question is, what can I do if I want to take a close look at an individual section but still I am interested in what’s going on around it? How can I combine details with the big picture when necessary?
And the answer is?
A new approach: a transformation interface which can be activated when needed. At peak times for instance, a running macro simulation will be connected to the micro simulation. The latter gets all necessary data from the macro model processing them a lot more precisely than the macro model would be able to. Then it returns everything to the macro model enabling it to show way more details than it would without the interface.
This way, you will no longer have to overload the macro or the micro model with something they are not made for. Just benefit from their individual strong points by hooking them to the interface when needed and letting the software take care of the communication – no matter which level you focus on.
Which will be the next step?
The software is already working and the joint simulation, if you want, will be validated and demonstrated not only in the Bosch use case but also in others because it is supposed to work for the product families and supply chains of any company.