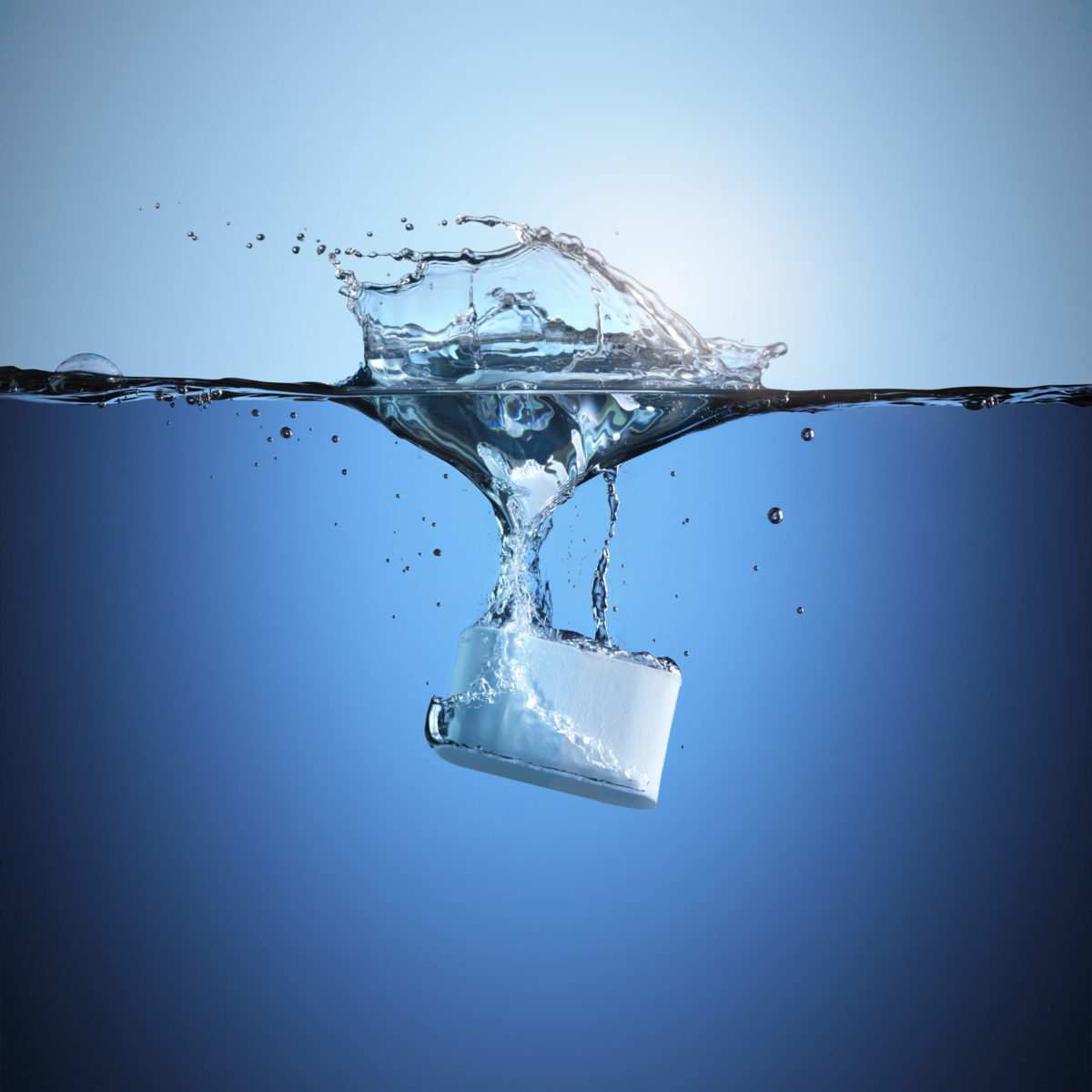
Prediction, online analyzing, sensors – Norwegians taking control
Be it for household detergents, personal care or institutional products, chemical precursors are not only expected to be produced on a top level, their quality must also be maintained when stored and shipped overseas or transported on a truck. Exposed to changing temperature, humidity or pressure, the delicate raw material may easily lump deep inside the big storage bags.
According to traditional anionic surfactant producer Unger from Norway, which also offers tailor made products for international customers, this is only one of the challenges typical for the chemical industry.
Apart from storage and transport, consistent quality is a challenge already during the production. In the so called neutralization loop, acid effects are elevated to appropriate pH values. Working half manually half automatically however, the results may slightly change depending on which operator is in the control room. On top, it takes up to 30 minutes to analyze samples in the lab.
From blind flights to full control for consistent quality
In order to get away from blind flight situations and to enhance the overall production, Per Olav Hansen decided to make his company become part of Productive4.0. It was on the topic of machine learning when he met Haugen Øystein, professor at Østfold University College (HIOF), who drew his attention to the project and the benefits of collaborating with partners. Together with the IT/software companies Prediktor and TellU and the research institution Sintef, they now form the Norwegian group in the project.
In the work packages (WP) 2, 4, and 5 and in a use case in WP 9 they are working on new digital techniques for a more efficient production, a predictable and better quality and real-time control. It is all about data collection, machine learning and simulation processes using online techniques and cloud solutions with the help of a reliable framework.
With Prediktor providing specific software and online spectroscopic instruments, Unger is about to enhance its analysis technology for the neutralization loop; NIR, a spectroscopy with near infrared light, allows a deep penetration of substances. Online, the collected data will be analyzed and automatically compared with the results of the local laboratory.
NIR will be integrated into simulation processes with digital twins and machine-learning approaches making the whole neutralization circuit predictable, more efficient and taking care of reliable results. Part of this is Grey Box, a model that combines machine learning tools and theoretical chemical equations. It allows potential settings and parameters, also for new virtual production test runs. Last but not least, shifting from half manual to sequence production, the latter will be completely preset ensuring the exact same results at any time. In this way, the operator in the control room can be way more confident that the right quality will be produced.
Of balls and lumps
And how will Unger control the condition of its stored and transported powdery goods before lumping? They simply put a ball in each of the bags, much like a tennis ball with cut out parts and a sensor inside. It measures relevant influencing factors like humidity, temperature and pressure. The values go through a gateway to the cloud provided by TellU. Together with Sintef which is supporting the integration of monitoring nodes it designed the ball’s specific architecture.
However, not only Unger will monitor its goods on the road. “We plan to share the transmitted data with our customers because high and stable quality is crucial to them”, Per-Olav Hansen says. And this is why we intend to use Arrowhead because it allows secure access to the data”. The University of Østfold will help to integrate the framework. The college team also develops an adaptive process simulator in the context of machine learning.