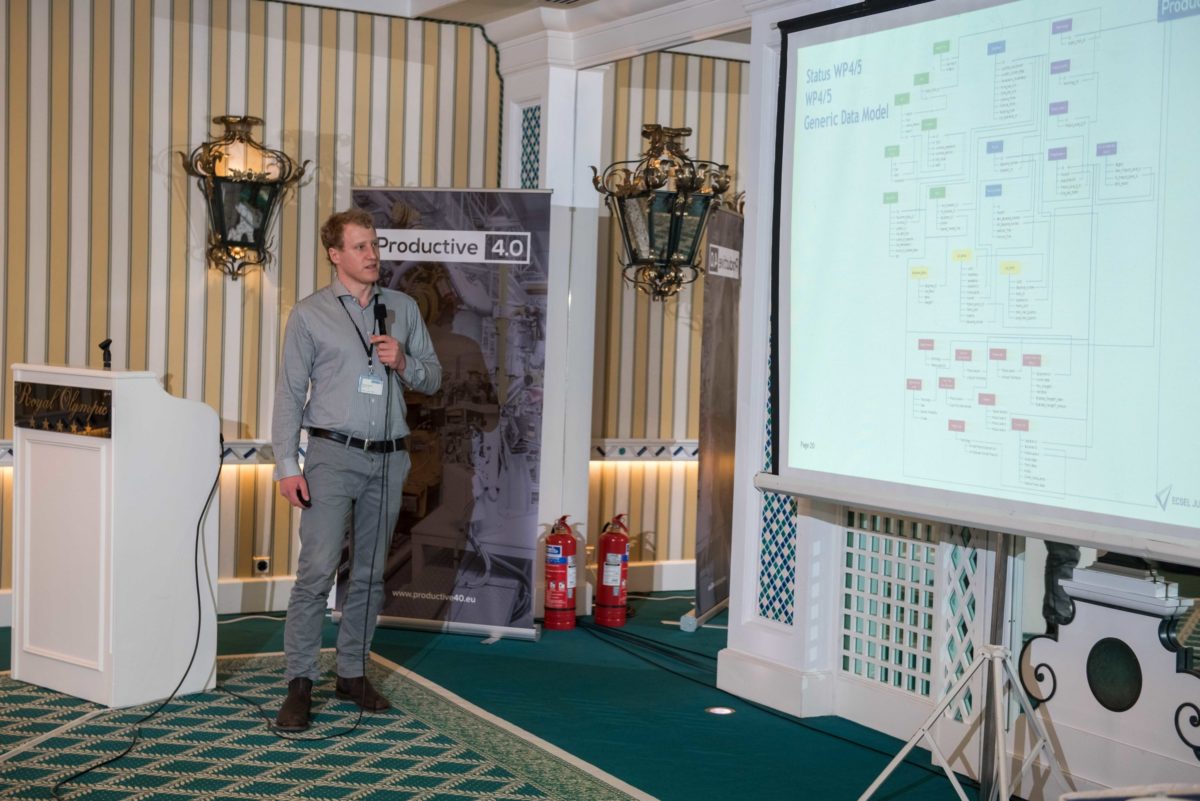
Supply Chain – Digital Twin and Generic Data Model
Big achievements in Productive4.0 were made in work packages (WP) 4 and 5. They are substantial for the project’s main aim: to create holistic operating systems reducing customer order waiting times, production lead times and improving an overall quality.
Avoiding asymmetric information and optimising processes, virtual company systems enable faster and far more flexible product life cycles. The virtual supply chain as a digital twin of the physical one allows for effective strategic decision making on different planning stages across the entire supply chain.
To that end, a digital twin with simulation models had to be developed, based on analytic models. Together with numerous partners, Bosch came up with two main Achievements in beyond-state-of-the-art Supply Chain Management.
Simulation-based supply chain planning system
One is the hierarchical simulation-based supply chain planning system as the first to incorporate an entire semiconductor supply chain in one planning system. It is based on a simulation system, which enables the planning results to be stable concerning production fluctuation and unexpected events.
An entire supply chain can be planned with this system, and the production plan can be tested and optimised in a digital twin. The latter helps to figure out the hidden effects of the aimed plan and thereby creates transparency in the complex supply network. The system is validated and tested at the semiconductor supply chain of Bosch.
Being extremely complex, the field of semiconductor production serves well as a blueprint for most other industrial domains. This also underlines the value of the other achievement resulting from collaboration of semiconductor partners Bosch, Infineon and ST-Microelectronics.
Generic Semiconductor Data Model
It is the Generic Semiconductor Data Model which represents the structure of a typical semiconductor supply chain in a database format. Following this system, a database was structured and filled with real production data from various semiconductor manufacturers. The database can be the generic basis for collaborative planning approaches among external supply chain partner companies.
The partners involved were motivated by the need of referring their manufacturing planning and control approaches to a generic semiconductor data structure. Using an agreed generic data structure enables the operational collaboration among different production partners avoiding individual data exchange. Shared planning approaches can be developed on this basis which covers all production partners collaborating in the supply network.
The common idea of a generic data structure was to simplify the collaboration of production partners considering intellectual property rights of the single companies. With an agreed data model defining how the data should be organised and structured in the single production sites, the collaboration on shared supply network planning approaches is simplified, as it is no longer necessary to transform and exchange data to the specific requirements of the individual planning approaches. In addition the collaboration with research institutes and software providers would be tremendously simplified as each external party can refer its provided approach on the commonly accepted generic data model. Thereby it can on the one hand be guaranteed, that the assumed data structure exists in each production site and the implementation of a provided solution is easily manageable.
On the other hand, external parties can get an overview of the current manufacturing and planning structure and the planning problems within the semiconductor industry. On basis of the generic data model it is possible to launch benchmark studies or software provider competitions. All these options end up in an improved manufacturing and planning environment with better and more suitable as well as generically usable software components.
Gate opener for collaborative supply chain management
To prove the concept and provide useful data based on this approach several use cases were defined by the partners applying the generic data model. The use cases ranged from Scheduling problems to green supply chain optimisation problems to manufacturing simulation tasks. Each use case requires a specific subset of the data model. On this basis, external research institutes or software providers are enabled to develop suitable solutions for typical planning problems in the semiconductor industry.
The achievement can be seen as a gate opener for collaborative supply chain management. It is the first time that the collaborative effort was driven to find a common, generic way to describe typical semiconductor fabs, products and workflows. The effort was motivation for the ECSEL follow-up “Communication and Support–Action” Project SC3 which started in October20.
Further – together with WP6 (standardisation) – it is intended to bring forward the Generic Semiconductor Data Model to the Industrial Data Standardisation Group in ISO (ISO TC 184 SC4) to complement ISO 10303 with respect to semiconductor data models.
The fusion with the Digital Reference Platform ontology of WP7 in Productive4.0 will channel the Generic Semiconductor Data Model to an even broader community and will help to make it vivid beyond the projects end.